MI Career Spotlight - Precision Machinist
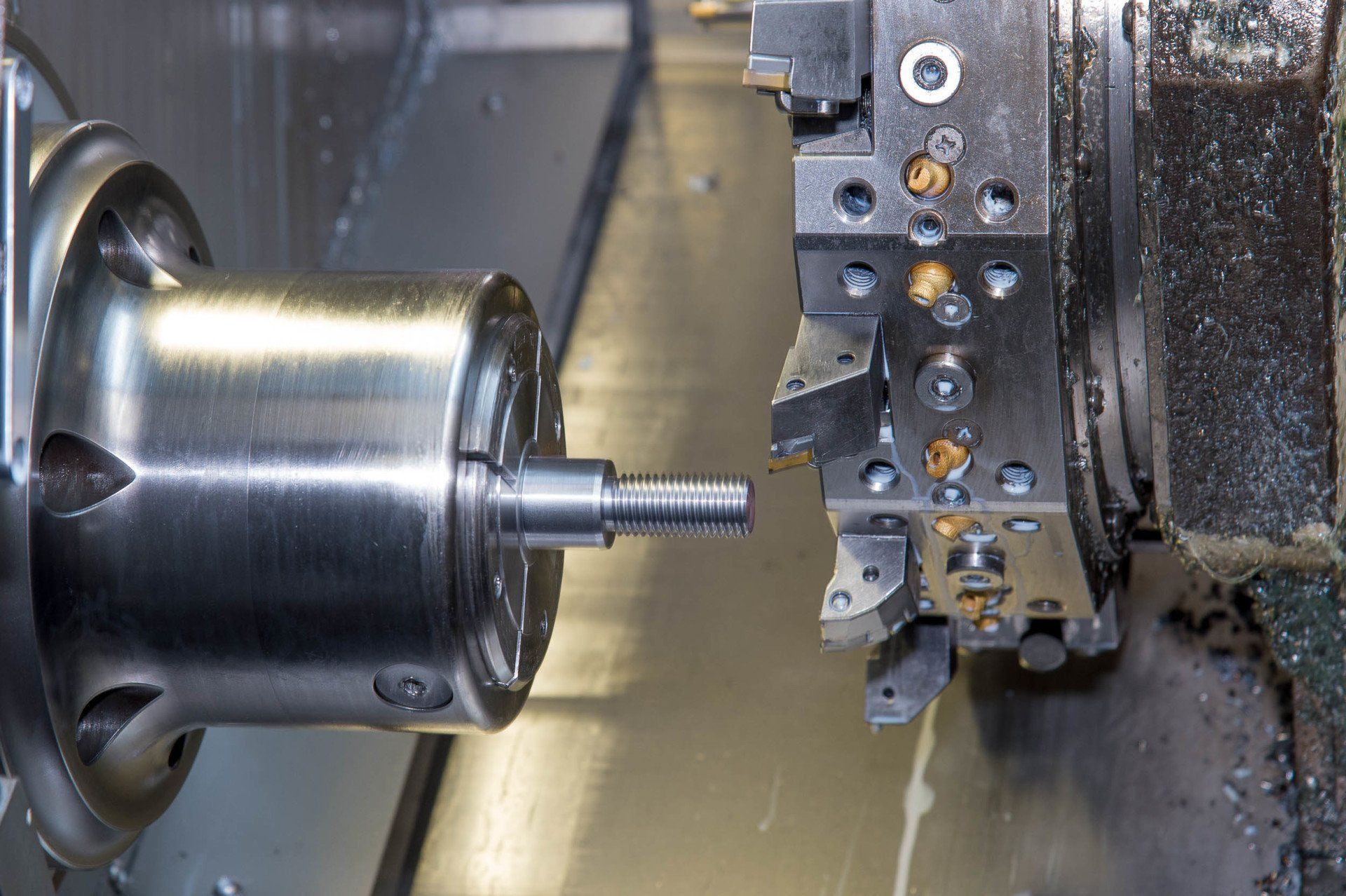
Machinists oversee maintenance, repair, and production work using a variety of tools that are conventionally controlled or computer numerically controlled (CNC), such as lathes, milling machines, and grinders, to produce precision metal and plastic parts. Although they may produce large quantities of one part, precision machinists often produce small batches or one-of-a-kind items.
Because the technology of machining is changing rapidly, machinists must learn to operate a wide range of machines. Although some of the computer controls are similar to those of other machine tools, machinists must understand the unique capabilities of these different machines. As engineers create new types of machine tools, machinists must constantly learn new machining properties and techniques.
Precision machinists typically do the following:
- Work from blueprints, sketches, or computer-aided design (CAD) or computer-aided manufacturing (CAM) files
- Set up, operate, and tear down manual, automatic, or CNC machine tools
- Calculate dimensions using measuring instruments
- Install, align, secure, and adjust cutting tools and workpieces
- Monitor the feed and speed of machines
- Turn, mill, drill, shape, and grind machine parts to specifications
- Measure, examine, and test completed products for defects
- Deburr all surfaces of parts or products to ensure that they conform to specifications
Demand for Precision Machinist
Today there are 28,000 machinist jobs in Michigan, an increase of 5,000 since 2009. In addition, 21 percent of current machinist are over the age of 55 and will soon be retiring out of the workforce. This will create a lot of job openings, even though future job growth is projected to slow down. Entry pay rate for Michigan machinists is $13.10 an hour and goes as high as $29.80 an hour.
Despite automation advancements in manufacturing technologies, machinists will still be required to set up, monitor, and maintain automated machining systems. In addition, employers are expected to continue needing machinists who have a wide range of skills and are capable of performing modern production techniques and almost any task in a machine shop. Manufacturers will continue to rely heavily on skilled machinists as they invest in new equipment, modify production techniques, and implement product design changes more rapidly.
What is Needed to Become a Precision Machinist
A high school diploma or GED is the minimum requirement for machinist education. During high school, students can prepare for careers in machinery by focusing their studies on subjects such as math, metalworking, drawing, and computer science. Postsecondary degrees are not required, but some form of occupational training is necessary. Machinists must be expertly familiar with their tools to ensure accuracy, so whether training programs are formal or informal, they should focus on hands-on, technical experience with metal-cutting and measuring machinery.
Machinist apprenticeship programs are available through community colleges, vocational schools and metal parts companies. Apprenticeships can last as long as four years and provide beginning machinists with full-time, paid training in metal shops. US Department of Labor Registered Apprenticeships award certificates that are recognized by companies across the US. Apprentices interpret blueprints and practice using basic equipment, such as lathes, saws and grinders, under the supervision of skilled machinists. These programs also incorporate lessons in the classroom, such as instruction in math, drafting and shop safety.
According to the U.S. Bureau of Labor Statistics, an increasing number of precision machinists are gaining vocational training in associate's degree programs. Available at community colleges and technical schools, 2-year degree programs in machine technology prepare students for entry-level positions in metalworking. After obtaining employment, machinists with associate's degrees are usually required to continue training on the job.
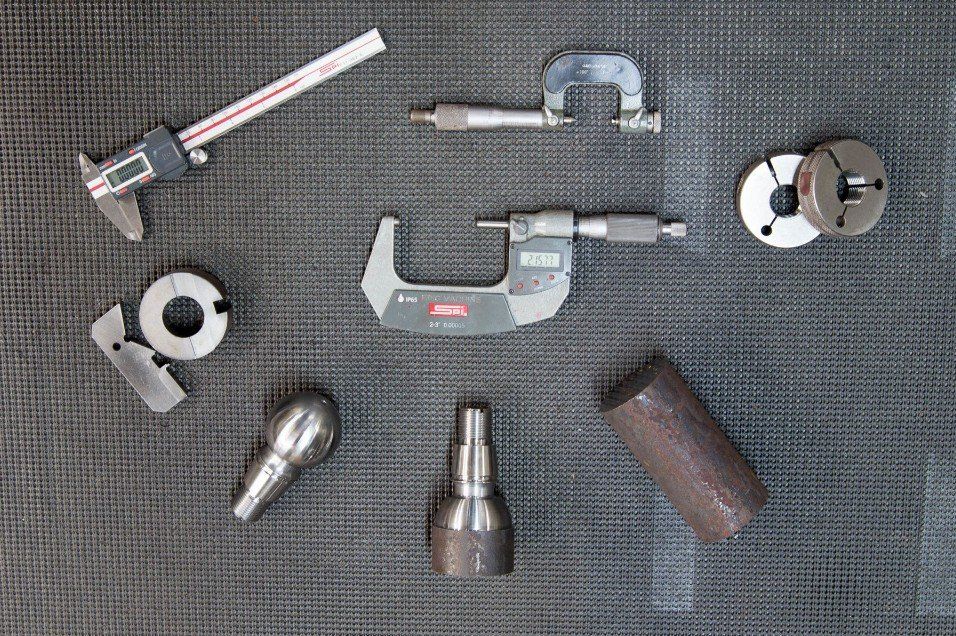